Finding the ice cream packing sweet spot
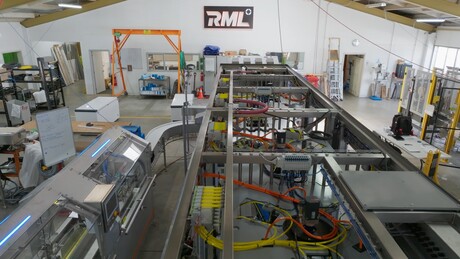
RML Machinery recently partnered with SMC Corporation New Zealand on the design and build of a fully integrated packing line for ice creams. The packing line was produced for a longstanding customer of RML, and New Zealand’s most loved ice cream brand, Tip Top.
“Tip Top has purchased four machine systems from us in the past. Due to the success of our past collaborations, we were selected to work on their latest project,” said Sales and Marketing Manager for RML Jon Marden.
The brief was to design a system that could erect, load and close four different carton sizes and feed these into a case packer with the ability to pack the cartons into five shipper SKUs at a rate of 300 ice creams per minute.
Unique to RML is the use of Codian robots and Gocator 3D vision systems. The Codian robots hit linear speeds of 5000 mm/s and can go up to 7000 mm/s, while the Gocator 3D vision systems are a progression for RML. “Typically, we will use a 2D system for applications like this but found the 3D system gave us better results across the range of ice creams,” Marden said.
Project challenges included the range and speed of the carton erecting and closing.
“In addition, everything needed to fit into a small footprint and the team was up against delivery challenges due to global supply chain issues,” he added.
Adding to this was the concurrent building, testing and commissioning of four complex machines, and ice creams are also challenging to work with in the testing phase.
“The delicate nature of the chocolate skin on the bars meant we had to be as gentle as possible — despite needing to process 300 ice cream bars per minute,” Marden said.
It is critical that the ice creams are only held in the machine very briefly, as they degrade quickly if they are not packed and sent to the blast freezers within a set time period. Logic was therefore written into the systems’ code to ensure the delivery of cartons from the loader through to the case packer and into the freezers was balanced to ensure the product quality is maintained.
For this project, RML turned to SMC Corporation. “We were in search of a custom vacuum head solution for the high speed pick-and-place robots and looked to SMC because of our long-established relationship and their customer-centric approach,” Marden said. “As was the case for all of our projects, the team from SMC were involved from the design process right through to testing and commissioning. The team was quick to respond as we needed them — at times going the extra mile to supply urgent parts to keep us on track.”
“We were thrilled to be part of this exciting project,” said Laurie Hamilton, National Field Sales Manager for SMC Corporation New Zealand. “In this instance, RML required a high number of outputs for the machine so SMC’s EX600 fieldbus system was selected for the job. Another clever idea that we had was to colour-code the tubing to differentiate between the extension and retraction functions.”
Hamilton added that all parts were engineered locally and that the team was on call throughout. “Our on-the-ground support team made sure that we provided comprehensive support and communicated throughout the process. This made all the difference,” he said.
Detailing the components used, Hamilton shared that the flexi-picker, designed with a custom robotic vacuum head, made use of the ZP3P series of blue vacuum cups from SMC. Every station is also equipped with: SMC’s SY EtherCAT compatible control solenoid valves, the TU series of polyurethane two core tubing to assist in the easy identification extension and retraction of air lines during fault finding and maintenance, and the D-M9 series of solid state autoswitches with a pre-wired M8 connector.
“Other components include the ZP3E series of vacuum cups, the MGPM guide cylinder, the CP96 cylinder, the CQ2 range of compact cylinders, safety rated air service units and more,” Hamilton added.
“Our biggest challenge on any new project is to get to grips with what the customer wants and understand the brief so that we can narrow down the correct solutions,” Hamilton said, reflecting on the project. “We want to reduce the testing time for the customer and try to nail it as close to right as possible, the first time round.”
Phone: 1800 763 862
Emerson AVENTICS Series XV pneumatic valves
Emerson's AVENTICS Series XV pneumatic valves are designed with interoperability in mind.
Festo VTEP proportional valve terminal
The VTEP proportional valve terminal uses high-precision piezo valves to reduce compressed air...
Kaeser CSG.1 oil-free rotary screw compressors
The CSG.1 rotary screw compressors have air flow rates ranging from 4 to 15 m³/min and...