Bottled water company quenches its thirst for high-pressure air
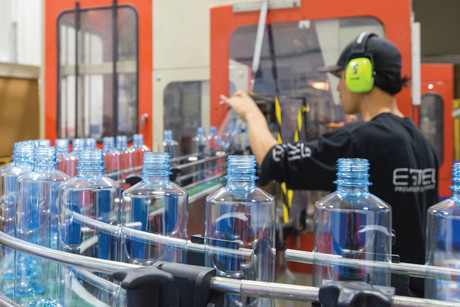
E’stel Water is a premium alkaline water that is sourced and bottled in Nelson, New Zealand. The artesian water comes from the snow-capped mountains of New Zealand and travels underground, 895 metres below the surface of the Waimea Plains, where it filters through various minerals. E’stel then extracts this high-alkaline water, before transporting it to a modern purpose-built bottling plant, where it is bottled, capped, labelled and packed ready for global distribution.
The uniquely shaped plastic bottles that this high-alkaline water is packaged in are manufactured on-site using a PET blow moulding machine. As demand for E’stel Water has steadily grown since the company was established just three years ago, so have the requirements for the bottling plant. This led to the recent investment into a much larger capacity PET blow moulding machine.
Responsible for manufacturing the water bottles, the PET blow moulding machine relies on an efficient supply of compressed air. At certain points within the process, compressed air needs to be pressurised up to 40 bar. This inflates the soft PET (polyethylene terephthalate) plastic into a mould cavity which takes the desired shape and size of the water bottles. With a standard industrial compressor reaching around a 10 bar pressure, a booster compressor is therefore additionally required at those points in the production process where this high-pressure compressed air is required, to boost the air pressure up to the desired level of 40 bar.
The new PET blow moulding machine at E’stel is able to blow a staggering 11,000 bottles per hour (BPH). As it is a much larger system than what the company had previously, a new compressed air system was therefore required to meet this increased demand for compressed air.
Wayne Herring, co-founder and director of E’stel Water, called on existing and local compressed air specialist PSL Total Air to present a suitable solution. In order to meet both the low- and high-pressure compressed air demand of the new PET blow moulding machine, PSL recommended and subsequently installed a complete compressed air system that included a Kaeser CSD 105 rotary screw compressor and a Kaeser DN 22 series booster.
The DN 22 booster comes as a compact, plug-and-play turnkey package. These completely unique integrated booster systems are delivered and configured to provide a system that is ready for immediate use.
All DN series Kaeser boosters are equipped with premium efficiency IE3 class drive motors which comply with and exceed prevailing Australian GEMS regulations for three-phase electric motors. Along with the generously dimensioned axial fan, which also assures reliable temperature control, this contributes to the booster’s cost-effective energy usage.
For all-round reliability, the DN series of boosters from Kaeser also come with an integrated Sigma Control 2 controller as standard, which delivers efficient control and monitoring of the compressor operation. This greatly simplifies the diagnostics process for precision service and maintenance work. They can also be connected to a monitoring system, such as the Sigma Air Manager 4.0 master controller, allowing full integration into an Industry 4.0 environment.
The DN series of boosters from Kaeser are available with initial working pressures of 3 to 13 bar with final working pressure 10 to 45 bar, motor power 22 to 45 kW and free air deliveries 2.9 to 19.6 m3/min.
“We already had two standard-pressure Kaeser Aircenter compressed air systems being used for various other pneumatic applications within the facility, so we knew these compressors were reliable — something that is very important to our operation,” said Herring. “When we started researching high-pressure compressed air solutions, a lot of products on the market seemed to be manufactured using quite dated technologies, and the replacement of parts would have worked out to be very expensive. With the Kaeser DN 22 booster we were presented with a cost-effective and state-of-the-art packaged solution.
“PSL was able to tailor a compressed air supply system to meet our exact needs, and it is already proving to deliver an energy-efficient and reliable supply of compressed air on demand. Their after-sales service has also been fantastic.”
Phone: 1800 640 611
Emerson AVENTICS Series XV pneumatic valves
Emerson's AVENTICS Series XV pneumatic valves are designed with interoperability in mind.
Festo VTEP proportional valve terminal
The VTEP proportional valve terminal uses high-precision piezo valves to reduce compressed air...
Kaeser CSG.1 oil-free rotary screw compressors
The CSG.1 rotary screw compressors have air flow rates ranging from 4 to 15 m³/min and...