Converting a steel mill to climate-neutral steel production
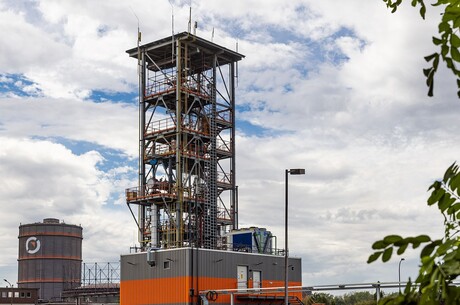
Steel has many useful qualities and is found in virtually all products where strength, malleability and stability are key properties. Whether in buildings, vehicles, machines or household appliances, steel is an indispensable component. However, steelmaking is an energy-intensive and carbon-intensive process with global average energy intensity of 19.76 GJ/tonne of steel and CO2 emission intensity of 1.83 tonne CO2/tonne of steel. The steel industry consumes 5.9% of global energy and emits 6–9% of global CO2 emissions.1 This is partly due to the use of coke, which is required in blast furnaces to remove oxygen from the iron ore and to extract the pig iron.
To decarbonise steel production and its high carbon dioxide emissions, Fraunhofer researchers and other partners are working on converting an existing steel mill to climate-neutral production methods. The aim is to produce steel by the direct reduction of iron ore with hydrogen, which would completely replace harmful coke as a reducing agent.
Work has been underway to develop new technologies to decarbonise production for years. The Fraunhofer Institute for Ceramic Technologies and Systems IKTS, the partner institutes Fraunhofer Institute for Systems and Innovation Research ISI and Fraunhofer Institute for Environmental, Safety and Energy Technology UMSICHT as well as Salzgitter AG are focusing on hydrogen-based direct reduction. During direct reduction in a reactor, the iron ore reacts with hydrogen at a high temperature. This hydrogen acts as a reducing agent and removes the iron oxide from the iron ore. What remains is the raw pig iron.
“By using electricity from renewable energy sources, the production of hydrogen is completely free of CO2 emissions. This means that by implementing green hydrogen in crude steel production, we can save up to 97% of harmful carbon dioxide,” said Dr Matthias Jahn, head of the department for Energy and Process Engineering at Fraunhofer IKTS.
In principle, green hydrogen is produced using electrolysis, where an electrical voltage is applied to split steam into hydrogen and oxygen. In particular, high-temperature electrolysis based on solid oxide electrolysis cells (SOEC) has had a long history at Fraunhofer IKTS. Given that the waste heat from high-temperature processes can be used to increase the electrical efficiency, this offers considerable advantages compared to other electrolysis processes — especially in steel production. Fraunhofer IKTS researchers have developed in-house electrolysis cells and stacks and used their own operating data for the techno-economic assessment of the process concept.
The consortium has demonstrated the feasibility of the new process in the BeWiSe follow-up project, in which the researchers and their industrial partners are now further optimising the entire process chain for resource and energy efficiency. For this purpose, a direct reduction demonstration plant measuring approximately 30 m in height on the Salzgitter AG premises is also used. For example, the project is investigating how biogenic materials can be used as a substitute for coal and natural gas to adjust the carbon content required in steel. Considering that large quantities of water are required for electrolysis during the production of green steel, the project is also focusing on how to optimise the use of water. As a result, the water formed during iron ore reduction with hydrogen is to be processed as far as possible for reuse.
The researchers are contributing all of their expertise, which ranges from high-temperature electrolysis, membrane processes for gas separation and water treatment to process simulation and plant modelling using digital twins.
“We are not satisfied with simply providing selective solutions and laboratory plants. We aim to offer Salzgitter AG comprehensive technological support for all process steps,” said Gregor Herz, group manager for Modeling and Simulation at Fraunhofer IKTS.
Dr Alexander Redenius, head of Resource Efficiency and Technology Development at Salzgitter Mannesmann Forschung, said: “We have been working successfully with the Fraunhofer researchers for six years to transform steel production. The direct reduction demonstration plant enables us to optimise the reduction process and how it interacts with the other process steps. Through this work, we are creating the basis for sustainable steel production with low CO2 emissions.”
The company aims to convert a third of its steel production to the climate-friendly process with hydrogen as early as 2026.
1. CO2CRC Limited 2020, Reduction of Greenhouse Gas Emissions in Steel Production.
Mettler Toledo oxygen measurement guide
Mettler Toledo has produced a guide for the process industries that explains the measurement...
Mettler Toledo pH sensors operating guide
Mettler Toledo has released a booklet describing good operating procedures for pH sensors, aimed...
Honeywell Process Solutions LEAP project services
Honeywell Process Solutions has launched its LEAP project services (Lean Automation of Automation...